Foam concentrate proportioning
NFPA 11 describes various types of foam concentrate proportioning equipment. In the following, three systems are looked at which are most common. Tight limits for the proportioning of foam concentrate apply to all of them.
The proportioning rate must not be less than the permitted values – i.e. 3% for a 3% foam concentrate or 6% for a 6% foam concentrate.
The proportioning rate must not exceed 30% above the permitted value i.e. 3.9% for a 3% foam concentrate or 7.8% for a 6% foam concentrate; respectively, the proportioning rate is allowed to be an absolute maximum of 1% above the permitted value – i.e. 4% for a 3% foam concentrate or 7%
for a 6% foam concentrate (the smaller value does apply).
To guarantee correct proportioning, the proportioner, including the proportioning rate must be tested at least once per year and its correct functioning must be checked.
Bladder tank with proportioner
The bladder tank with a proportioner is a proven and cost-effective technology. The bladder tank is a pressurized vessel with a bladder inside which is filled with foam concentrate. The tank is pressurized with water from the fire extinguishing line and discharges the foam concentrate from the bladder as required. The bladder is connected to a proportioner which operates using the venturi principle. When the fire pumps are activated, pressure is generated by the pump, causing delivery of foam concentrate to the proportioner. As the extinguishing water flows through the venturi proportioner, the resulting pressure drop across the proportioner induces the foam concentrate into the extinguishing water flow. The advantages of this system are its simple design without moving parts and its easy operation. No external energy is required, and the system is relatively inexpensive.
A disadvantage is that the system is a pressurized vessel subject to corresponding regulations such as ASME Boiler & Pressure Vessel Codes. In order to refill foam concentrate, the system must be shut down and drained, resulting in significant down time of the system. The rubber bladder is sensitive; when damaged, water will contaminate the foam concentrate. At a given proportioning rate, the system is only suitable for low variations in the extinguishing water flow pressure and volume. Adding or changing individual foam discharge devices is possible only to a very limited extent. The system is also unsuitable for proportioning highly viscous foam concentrates.
To conduct any mandatory required annual testing, the system must be activated, and premix generated at the venturi proportioner within in the extinguishing water line. The correct proportioning rate must be measured in the premix by laboratory analysis. The generated premix must be disposed of. The consumed foam concentrate in the bladder tank needs to be replaced.
Externally driven proportioning pump with flow meter
The system consists of an atmospheric tank for the foam concentrate, an electric or diesel-powered foam concentrate pump with an electronically controlled valve and a flow meter in the extinguishing water flow line. When the fire pumps are activated, the foam concentrate pump drive and electronic control system must be activated. The extinguishing water flow rate is measured by the flow meter and the control system adjusts the correct foam concentrate quantity via the control valve. The foam concentrate is injected into the extinguishing water flow by the foam concentrate pump. If there is a change in the flow rate, the amount of injected foam concentrate is regulated by the control valve.
The system's advantage lies in the precise proportioning of the foam concentrate, independent of the extinguishing water pressure or flow rate. Foam concentrate can be topped up during the extinguishing operation. The system is capable of proportioning highly viscous foam concentrates. For the purpose of annual testing, the system must be activated; however, the delivered foam concentrate can be measured via a recirculation line back to the atmospheric tank. The proportioning rate is calculated from the extinguishing water / foam concentrate flow rate. No premix is produced; and as the foam concentrate is passed back into the tank, no foam concentrate needs to be refilled.
Disadvantages are the requirement for an external interruption-free energy supply for the foam concentrate pump and the control system, as well as the need for a sophisticated control system with more installed instruments, valves and accessories and the comparatively higher purchasing costs. Furthermore, it must be accepted that a delay occurs between the change of the extinguishing water flow rate and the newly adjusted foam concentrate amount. The foam quality may be compromised when constantly changing operating conditions as foam discharge devices are turned on or off or changed.
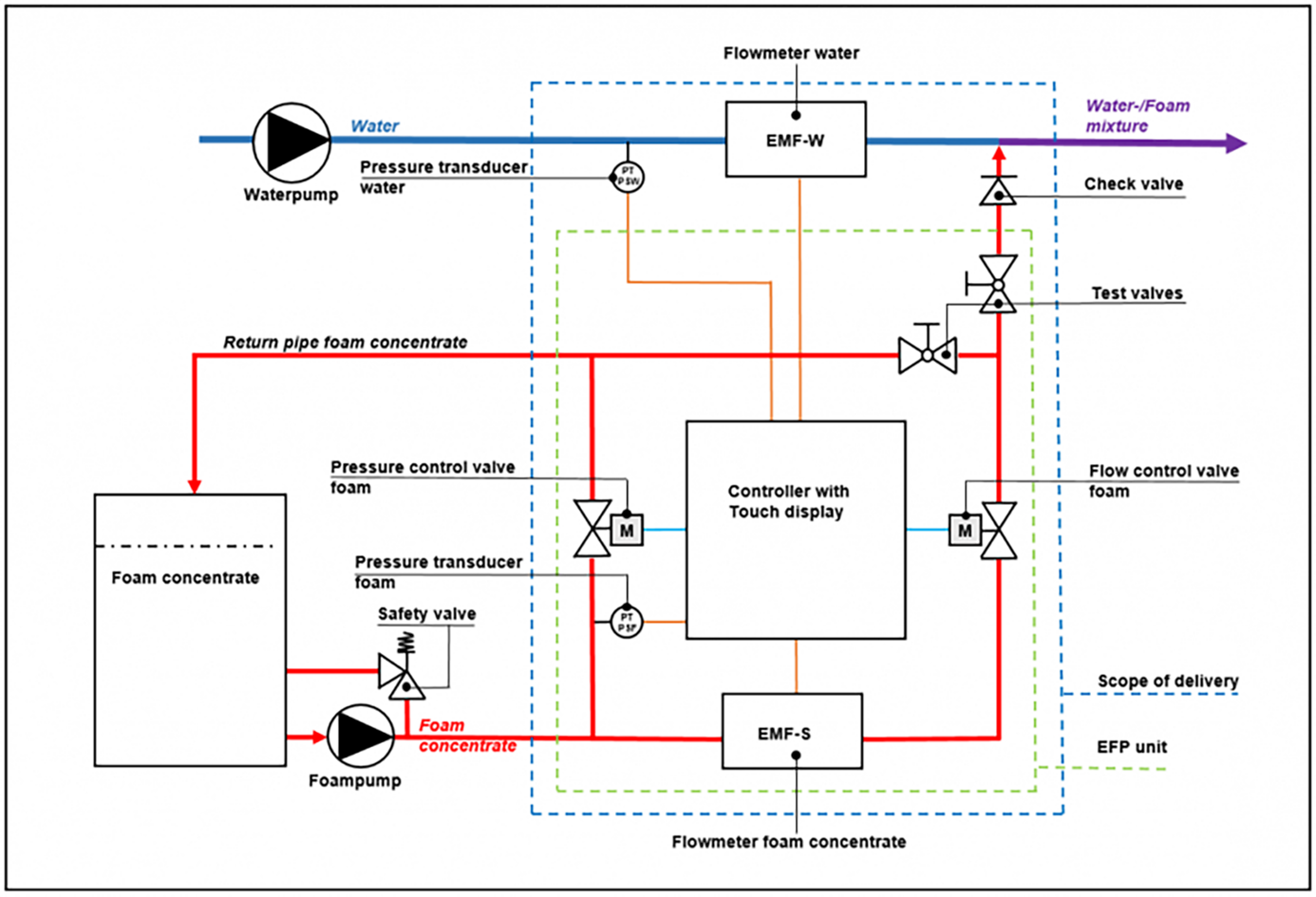
Externally driven proportioning pump with flow meter
Water motor with proportioning pump
The system consists of an atmospheric tank for the foam concentrate, a water motor installed in the extinguishing water flow line and a foam concentrate pump which is connected directly to the water motor. Water motor and pump form one compact unit. Upon activation of the fire pumps systems water flow, rotation in the water motor starts. The direct coupling to the foam concentrate pump provides immediate foam concentrate injection into the extinguishing water. If the flow rate changes, the amount of foam concentrate is adapted immediately.
The advantage of the system is its independence from external energy sources as well as a precise and immediate foam concentrate proportioning regardless of the extinguishing water pressure or flow rate. If a piston or plunger pump is used for the discharge of the foam concentrate, adjustment or calibration after installation is not necessary since the water motor and the pump are volumetric devices firmly connected to each other. Foam concentrate refilling during operation is possible. The system is also capable of proportioning highly viscous foam concentrates. The proportioning rate is calculated from the extinguishing water / foam concentrate flow rate. No premix is produced; and as the foam concentrate is passed back into the tank, no foam concentrate needs to be refilled and no expensive disposal of foam / water solution is required.
The system must be activated for annual testing; however, the delivered foam concentrate can be measured via a return line. The proportioning rate is calculated from the extinguishing water / foam concentrate flow rate. No premix is generated; and if the foam concentrate is passed back into the tank, no foam concentrate needs to be topped up. The larger design and the comparatively higher purchasing costs can be a disadvantage of the system.
With any system, consideration should be taken into account for the annual testing costs, which can be considerable in terms of replacement foam concentrate, disposal of premix and manpower.
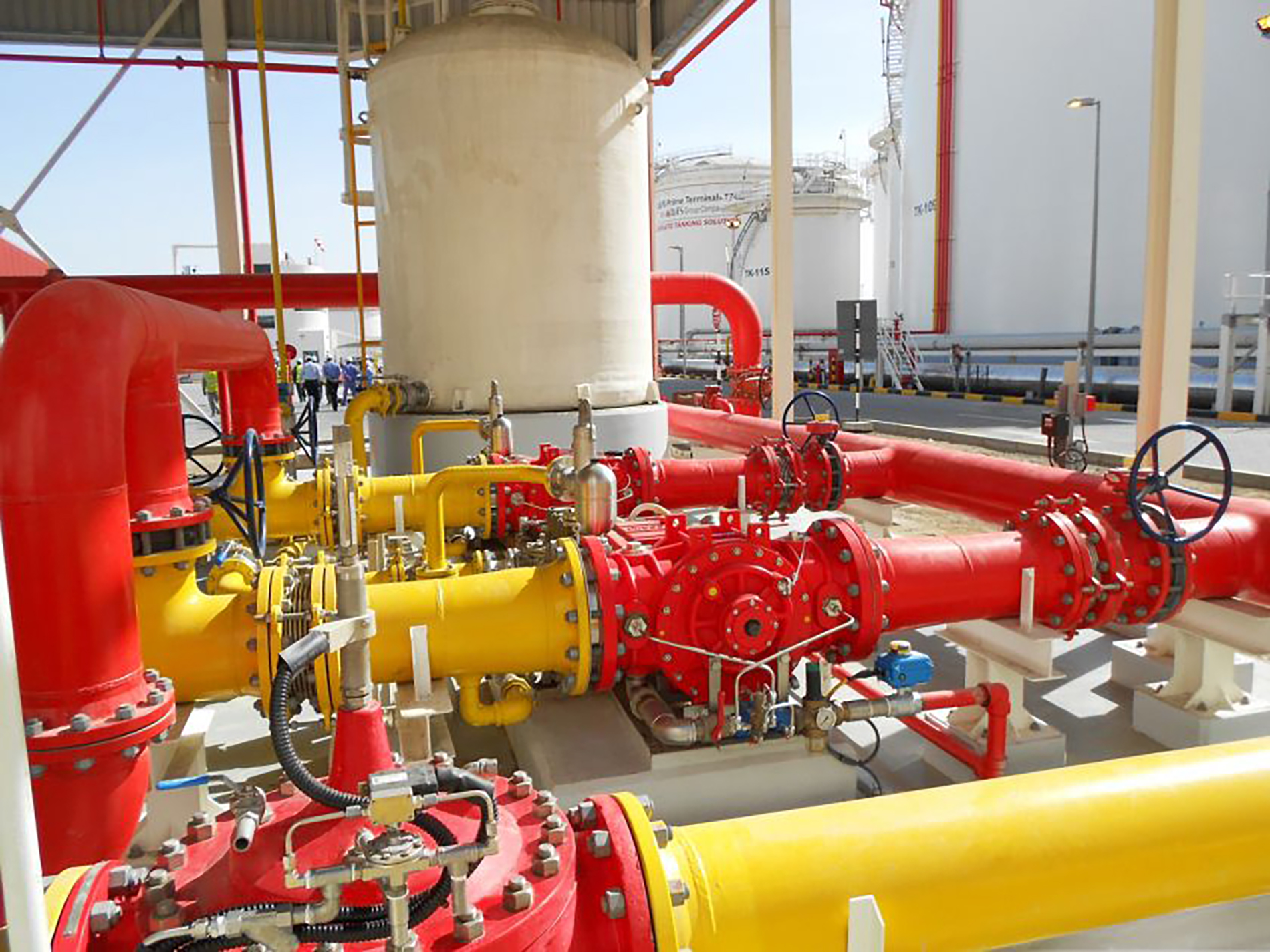
Water motor with proportioning pump
Mobile extinguishing systems
As the stationary foam discharge equipment can be damaged in extensive fires in the tank or in the dyke area and thus lose effectiveness, mobile fire monitors and foam pipes may be used.
Foam nozzles
Foam pipes are normally held by firefighters, making them very flexible. Yet they have only limited extinguishing agent flow rates and reaches.
Firefighting monitors
Firefighting monitors are discharge devices that can be permanently mounted in fixed applications or on vehicles or trailers and are available in many sizes. The extinguishing agent flow rate can be up to approx. 16,000 gpm and the reach can be up to 600 ft if the pressure of the fire pumps is sufficient. They are suitable to discharge foam, e.g., to extinguish a surface fire in a tank; or water, to protect exposures such as cooling a neighboring tank or the tank wall of a burning tank in order to prevent reaching the critical temperature for a boilover. The accumulation of water inside the dyke-area should always be observed to avoid an overflow of the dyke area.
Mobile fire monitors can be supplied either by the extinguishing water of the stationary fire pumps or by mobile pumps. The injection of the foam concentrate usually takes place via mobile proportioners. This clearly points towards the advantage of energy independence for water motor-driven proportioning pumps.
The strategic decision for the sizes of mobile units available as back-ups is shown by the following example for the placement of monitors for fire extinguishing at tanks which are 150 ft (45 m) in diameter and 50 ft (15 m) high. According to NFPA, 17,662 gpm of premix are required. This results in several alternatives for the monitors. Generally, foam concentrate proportioners should be able to handle varying flow rates to guarantee flexibility during extinguishing operations. Depending on the local conditions, the monitors will need to keep a minimum distance to the burning tank or may not be able to be positioned near to the tanks due to debris or fire ground operations. In addition, it will not always be possible to position several monitors around the tank. It must be ensured the monitor has sufficient throwing height in relation to the tank height, to deliver foam into the inside of the tank. The dimensioning of the entire firefighting system is made following legal regulations as well as recommendations by associations like NFPA and is not looked at more closely in the present article.
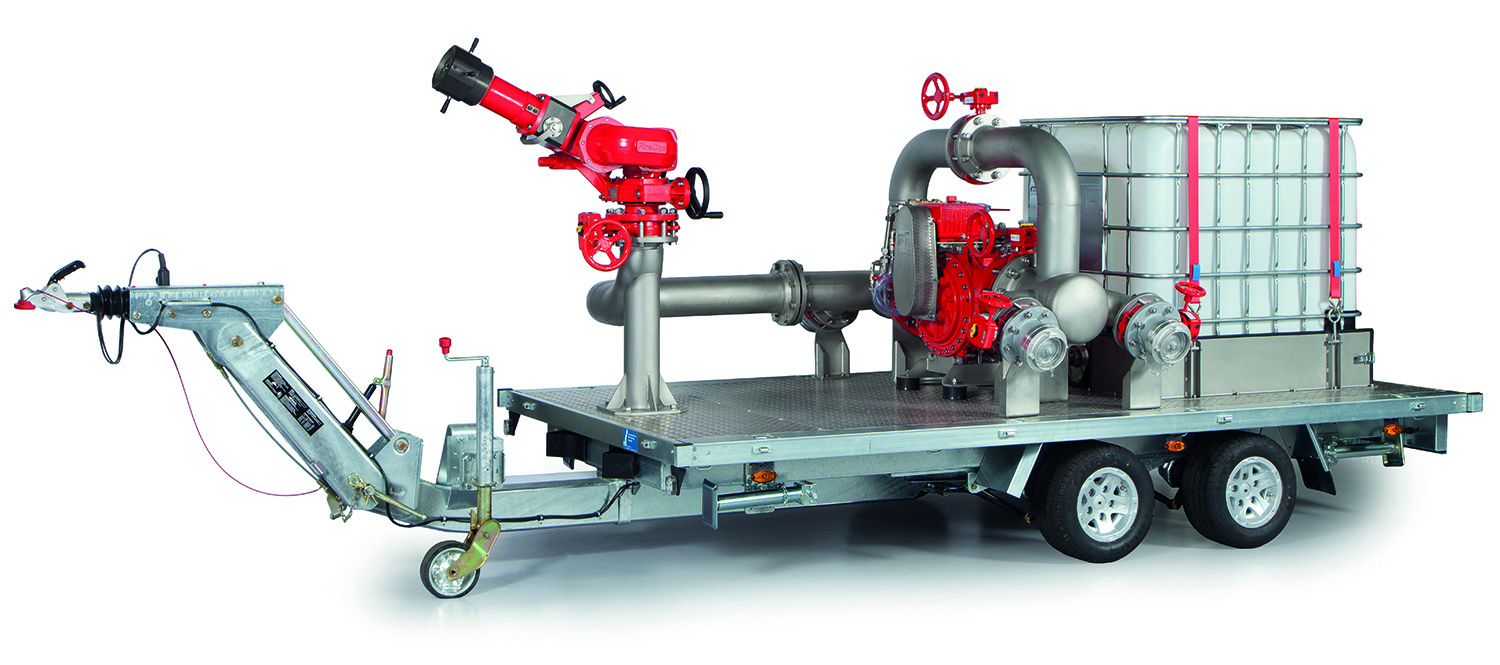
Trailer with FD8000 and M4 monitor
Fire monitor size | Quantity | Distance from tank [ft]* | Flow rate [l/min] |
M9 | 1 | 312 |
10,560 |
M7 | 2 | 263 | 5,280 |
M5 | 3 | 197 | 3,170 |
M4 | 4 | 148 | 2,113 |
* Distance between monitor and tank dependent on low rate
Lessons learned
As mentioned in the introduction, it seems that there are still lessons to be learned from disastrous fire incidents of past years. Tank farm fires in the oil and petrochemical industry do not happen frequently. When they do, they usually have devastating consequences.
It is very probable that large fires would be extinguished quickly if the warning systems worked as they were supposed to, if the suitable fire suppression system in the required capacity and performance would be installed and all equipment in place worked reliably. This leads to notably less damage than experienced in the named examples.
Summing up, the following points should be learned as a minimum. As far as they have not yet been implemented, or just partly, they should serve as a basis for discussions about one's own fire protection concept.
- Have a suitable fire protection concept including alternative scenarios which adapt to the given situation regularly.
- Always have a sufficient number of mobile extinguishing systems as a backup to fixed extinguishing systems.
- Stock a suitable foam concentrate.
- Ensure sufficient foam concentrate supply.
- Ensure sufficient water supply.
- Keep well-maintained, quickly and well-accessible, strategically correctly placed and functioning extinguishing equipment available in a sufficient number.
- Have trained personnel available in a sufficient number.
- Ensure a quick implementation of a suitable plan of action.
References
[1] National Fire Protection Association, NFPA 11 Standard for Low, Medium, and HighExpansion Foam 2005 Edition.
[2] U.S. Chemical Safety and Hazard Investigation Board (CSB), Factual Update Storage Tank Fire at Intercontinental TerminalsCompany, LLC (ITC) Terminal, Published: October 30, 2019.
[3] Nico Zorzetto PhD, Modern Safety Technologies on highimpact mega-fires, GULF FIRE, January 2020