CAF as an Extinguishing Solution for the Power generating Industry
The modern society we live in increasingly relies on a growing supply of electrical power. The electricity is most often produced by generators at a power plant, whereby the generators are primarily driven by combustion engines or nuclear power. In the last years alternative energies such as wind or water are increasingly being used as means to drive the generators. Another growing source for electric energy is solar power. In addition, our electricity networks are interlaced with transformers and substations. All these sources have in common, that they must be protected against the risk of fire to avoid any unintended interruption of operation.
About the Author
Frank Preiss is Managing Director of FireDos GmbH.
FireDos are experts in proportioners and monitors for firefighting, focusing on customer service and their in-house-developed leading technologies.
This article has originally been published in International Fire Fighter, September 2024.
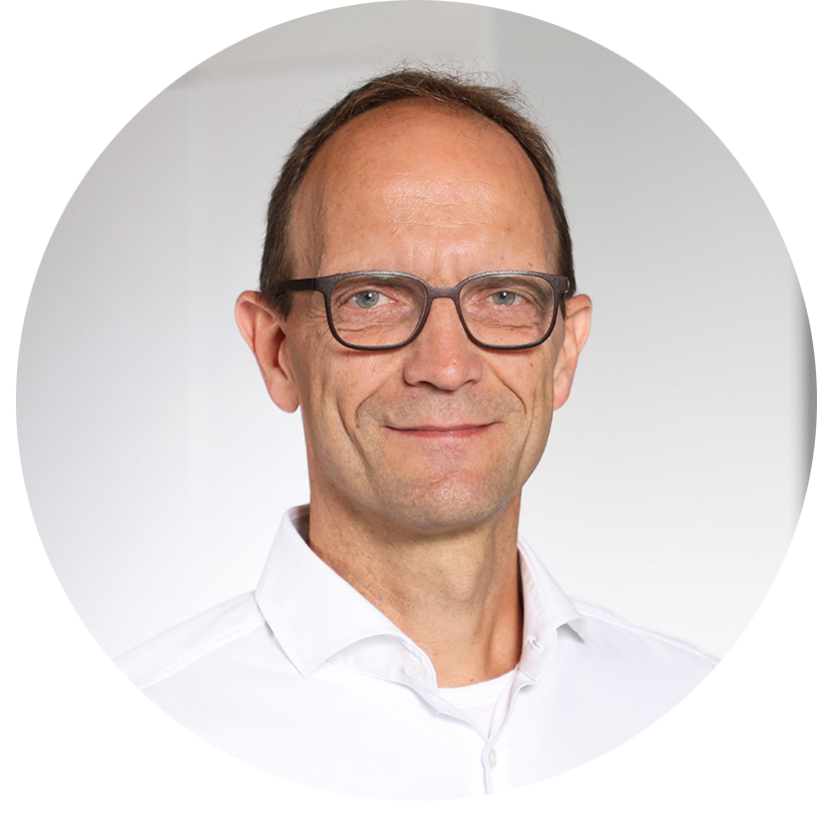
Frank Preiss
FIRE RISKS AND PROTECTION REQUIREMENTS IN THE POWER GENERATION INDUSTRY
Apart from solar power, the actual generation of electricity is achieved in the generators that are coupled to the rotational source by gear boxes. Their lubrication oil presents a significant fire hazard, particularly as generator surfaces and operating temperatures can surpass the oil’s ignition point. Even small generators, gear boxes and transformers may have hundreds of liters of oil, whereby large systems may require thousands of liters of oil for lubrication and cooling. In the event of an oil leakage due to a seal fatigue, a mechanical fault of material cracks, oil can leak and ignite on hot surfaces. The resulting fire can have catastrophic consequences for the installation or plant if no or only an inadequate fire protection system is installed.
The property and system damage alone can result in millions to tens of millions of dollars of cost. In addition, the system will be out of operation for months or years, depending on damage severity and the availability of spare parts or replacement components.
Wind turbines are in addition exposed to lightning strikes, faults in electrical equipment, sparks due to overloading of mechanical brakes and flammable work during maintenance and repair. Furthermore, the energy providing components are surrounded by flammable materials used to build i.e. the encapsulation or the rotor blades themselves and easy and quick access is not possible for extinguishing purposes.
Fires are relatively rare and exact statistics are not publicly available. Occurrence estimates vary from 1 in 2,000 to 1 in 20,000. At 1 in 2,000 this results in a 100% chance of a fire in a wind farm with 100 turbines during an operating span of 20 years. Even at 1 in 20,000 the chance lies at 10%.
For transformer fires published numbers also vary, but in practice, throughout a 40-year service life, 2.4% to 4% of all transformers should be expected to see a fire. In most cases, if the fire is not detected at a very early stage, transformer fires will nearly always result in a complete write-off. Even in this case a fire protection system is essential to protect the remainder of a substation installation, neighboring assets as well as to reduce the pollution and contamination of the environment.
Fixed installed fire detection and suppression systems will enhance the safety of the units and can provide a strong return of investment considering the associated replacement and downtime costs.
There are various systems that can be used to extinguish fires in power generating installations. Traditional sprinkler or deluge systems using water are impractical and do not have the same extinguishing effect as foam, especially when having to deal with lubrication oil fires. Clean agents or water mist have shown good results but may also not be the method of choice when having to deal with burning lubrication oil. Recent tests have shown that CAF systems have proven to be very effective for extinguishing fires in the power generation industry, specifically when having to deal with lubrication oil fires.
What is CAF?
CAF stands for Compressed Air Foam. This is a highly effective, very homogenous extinguishing foam produced through a specialized process.
Foam for firefighting purposes is made from three components:
- Water
- Foam concentrate (foam agent)
- Air
Water and foam concentrate are mixed in a very precise ratio. This mixture will make up a premix, which will generate foam once it is aspirated with air.
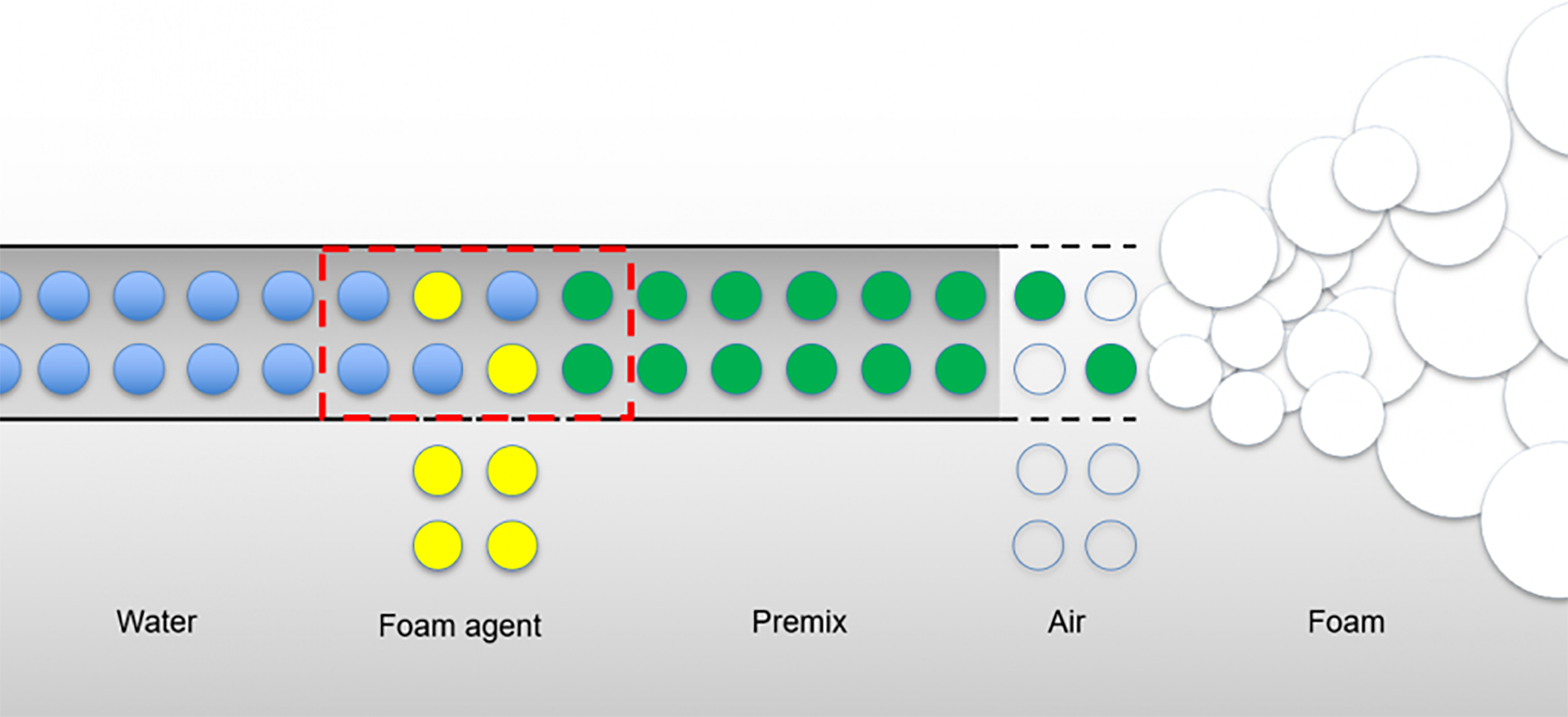
Components of firefighting foam
Water and foam AGENT combine to form premix
The premix is made by using a proportioning system. A commonly used proportioning system for CAF is the FireDos GEN III. The system consists of an atmospheric storage tank for the foam concentrate, a water motor installed in the extinguishing water flow line and a foam concentrate piston pump which is connected directly to the water motor. Water motor and piston pump form one compact unit. Upon activation of the fire pumps, rotation in the water motor starts. The direct coupling of the water motor to the foam concentrate pump affects immediate foam concentrate injection into the extinguishing water. If the flow rate changes, the amount of foam concentrate is immediately and automatically adjusted.
The advantage of the system is its independence from external energy sources as well as a precise and immediate foam concentrate proportioning regardless of the extinguishing water pressure or flow rate. Adjustment or calibration after installation of the system is not necessary since the water motor and the piston pump are volumetric devices firmly connected to each other. Foam concentrate refilling during operation is possible. The system is also capable of proportioning highly viscous foam concentrates.
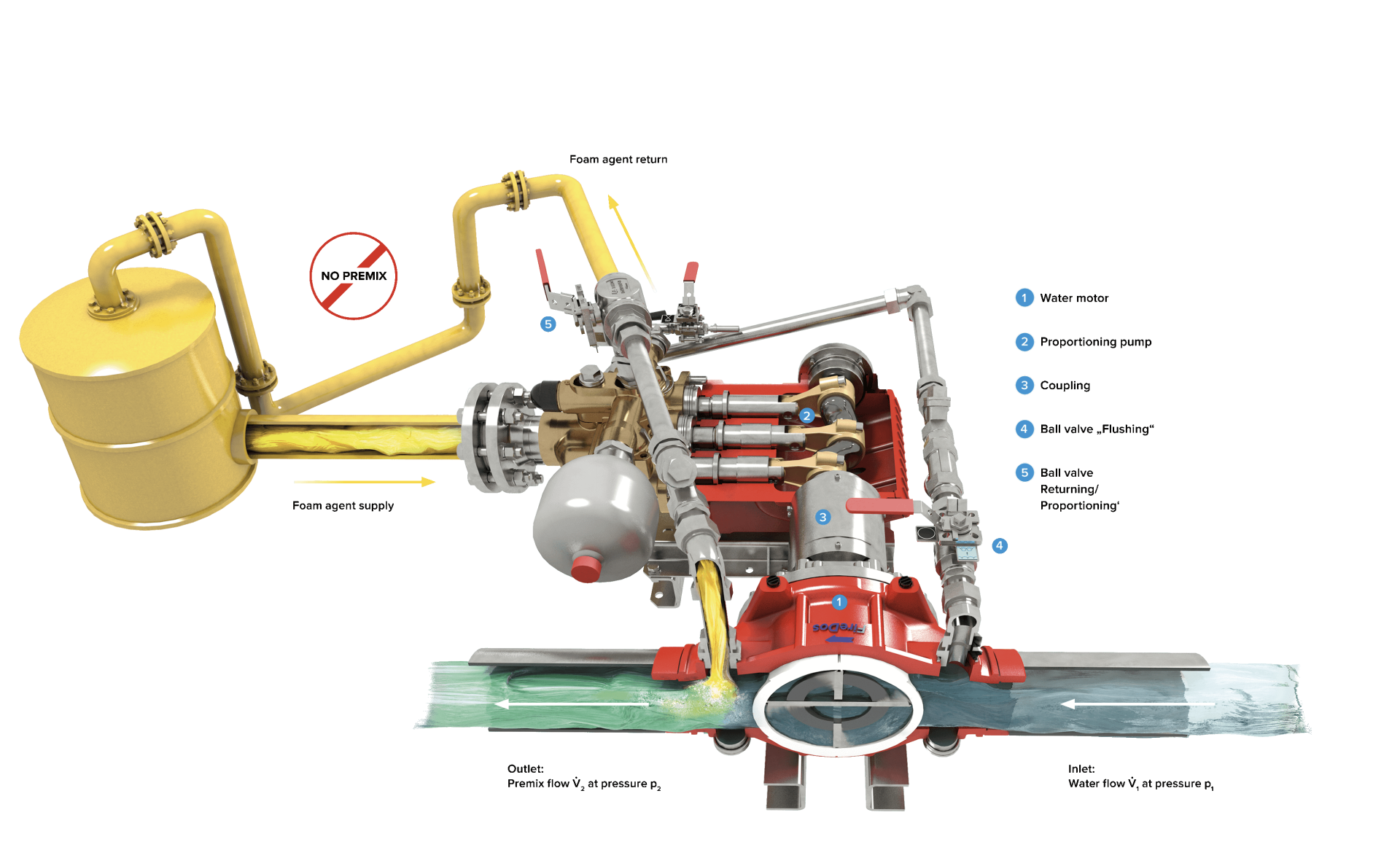
Schematic of the FireDos GEN III water motor coupled piston pump proportioner
Every proportioning system must be activated for annual testing; however, with the water motor driven proportioning pump, as designed and supplied by FireDos, the delivered foam concentrate can be measured via a return line and injected back into the storage tank. The proportioning rate is calculated from the ratio of the extinguishing water and the foam concentrate flow rate. No premix is generated; and if the foam concentrate is passed back into the tank, no foam concentrate needs to be topped up and no premix must be disposed of.
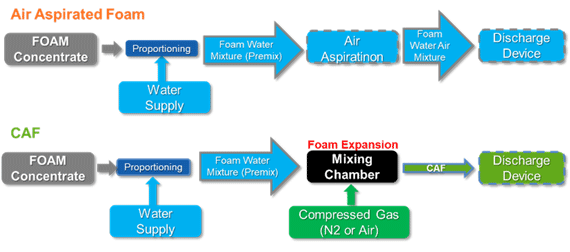
Generation process of conventional foam and CAF
Production of Firefighting Foam
CAF (Compressed Air Foam) is a unique foam making process that produces a homogenous finished foam of micro size bubbles. This foam making process will use either compressed breathing air or nitrogen gas. Compressed air and premix (foam/water solution) is brought together in a device known as a mixing chamber. In the mixing chamber the transition from liquid to foam takes place. In a CAF system an engineered finished foam is produced in the mixing chamber that is designed specifically for an applicator.
With a CAF system foam of a specific foam density can be generated. The foam quality of CAF is much greater than any other foam making process. CAF is a higher quality finished foam that gives fast control and extinguishment of fire with strong reflash protection. Vapor suppression with CAF is longer and more secure than with a traditional foam making process.
ADVANTAGES OF Firefighting FOAM PRODUCED WITH CAF
- The structure of the generated foam is more homogeneous
- The much denser and stronger foam blanket delivers improved extinguishing properties such as:
- Better back-burn resistance
- Higher prevention of a reliable emissions of flammable gases
- Higher prevention of a reliable intrusion of air to the flammable liquid
- Enhanced cover of the flammable liquid
- Longer hold time
- Excellent adhesive properties on surfaces
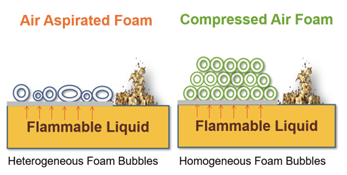
Comparison of conventional foam and CAF
CAF is incorporated in NFPA 11 in chapter 8. The application rate is significantly lower compared to conventional foam application rates and tests have shown, that the total amount of foam concentrate used to extinguish a fire was up to 70% lower. CAF can be utilized with AFFF, AR-FFF as well as fluorine-free foam concentrates. The most common applications are for solid metals, hydrocarbon liquids and polar liquids and solvents.
The CAF system from ACAF Systems used together with the FireDos GEN III proportioning system is FM approved under FM5136 and is being increasingly used in applications of the power generating industry.
Where is the advantage of using CAF in the power generating industry?
The main advantage lies in the small and efficient package design consisting of a CAF generator with Nitrogen pack, a foam proportioning system with an atmospheric foam concentrate tank, a water supply and the pipework and outlet devices such as CAF nozzles, foam chambers or fire monitors. The design is very flexible.
Fixed spray systems are designed to protect three dimensional objects as used for power generating installations. In this system design we are wanting to spay foam over all the surface areas of the object as well es onto the ground. This is the same principle that is used in water spray systems for the same application, but as CAF is more effective than water in suppression of flammable liquid fires, the CAF systems make for a sound solution whenever oils are in use. Due to the enhanced cover of the flammable liquid, the longer hold time of the foam, and the excellent adhesive properties on surfaces, CAF has advantages over water mist and clean agents, that will dissolve once the reservoirs have been depleted.
The CAF generator is simple to operate, with no moving parts and the FireDos GEN III proportioners are purely mechanical.
Other advantages of using the combined ACAF and FireDos system do not differ from the advantages standard firefighting foam installations are profiting from:
- Lower application rate equaling less foam concentrate and water needed
- Stronger foam means a faster control of the fire with a higher reignition protection and high adhesive properties
- All components are FM tested and approved
- The CAF system does not have any moving parts
- The proportioning system is purely mechanical – no electric power is required
- The system is designed also for use with high viscosity and fluorine free foam concentrates
- The system has a compact and versatile installation
- With the option of testing the proportioning rate without having to create premix or foam the system is cost-effective and environmentally friendly
Example of fixed installation CAF systems
The following example shows a fixed pipe ACAF CAF system using HDN-5 CAF nozzles. HDN-5 is a FM Approved stationary CAF spray nozzle designed for horizontal installation. This CAF nozzle is ideal for use in CAF fixed spray systems as used for the power generating industry. The unique ACAF patented central hub and spray nozzles gives the HDN-5 the greatest coverage area of any FM Approved CAF nozzles in the horizontal position. A 304 stainless steel body with brass spray nozzles is the standard construction, 316 stainless steel is available upon special request. Nozzle location and supply piping shall be in accordance with ACAF’s FM Approved Design Manual.
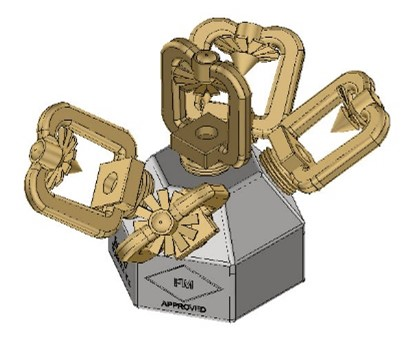
ACAF HDN-5 CAF nozzle
Example of a fixed pipe CAF system with open HDN-5 nozzles

CAF installation
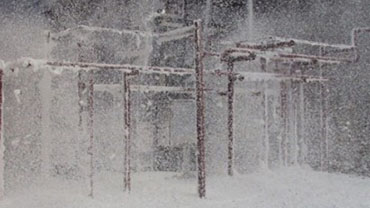
CAF installation while foam discharge
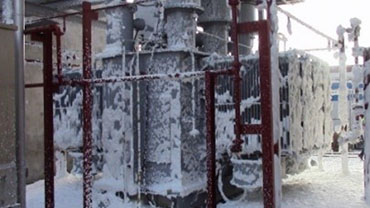
CAF installation after foam discharge
Conclusion
Fires in the power generating industry, though infrequent, present a significant risk for the plant operator, the community and the environment.
Understanding the fire hazard and the resulting consequences of an incident, and planning and implementing fire detection and suppression measures, are crucial for safeguarding the electrical infrastructure and ensuring the continued safe and reliable delivery of power. The use of a CAF system is one dependable option to reach this goal.
For more information on CAF systems and the water motor driven proportioning technology, visit acafsystems.com and stationary proportioning systems from FireDos.
This article was originally published in Gulf Fire, April 2024.
THIS MIGHT ALSO BE OF INTEREST FOR YOU:
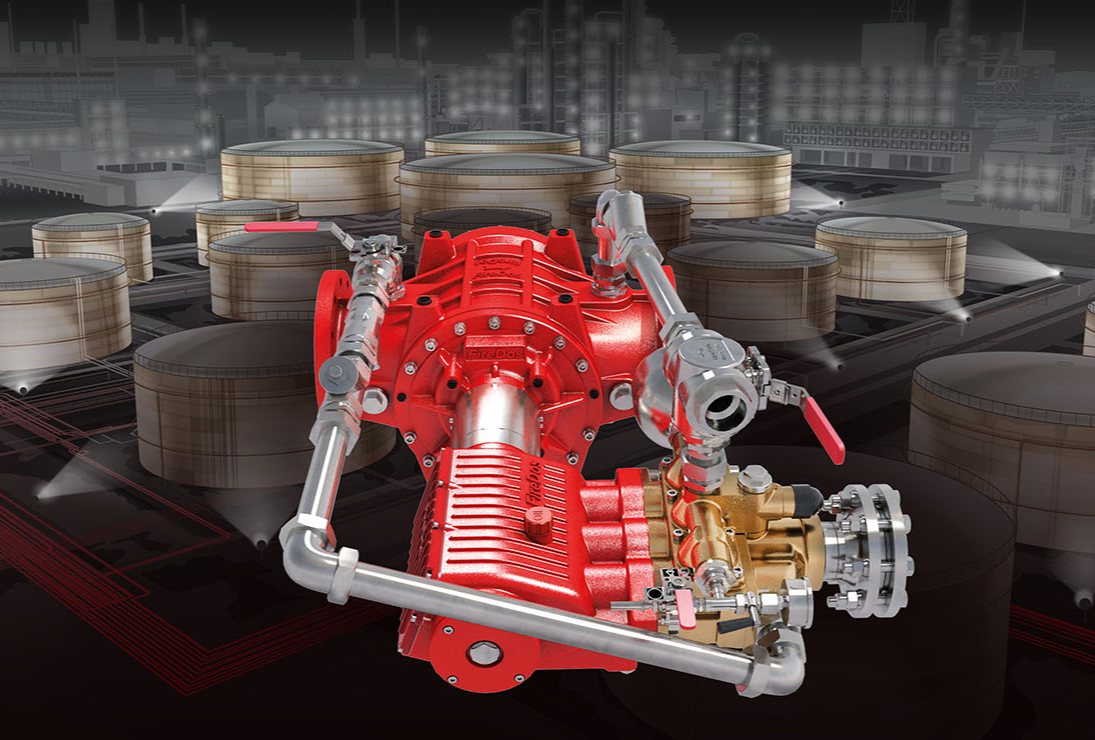
Stationary foam proportioners
Reducing costs, enhancing performance - explore the advantages
View more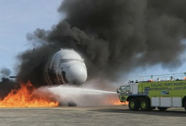
Compressed air foam in airport firefighting
Enhancing the extinguishing capability of airport firefighting vehicles
View more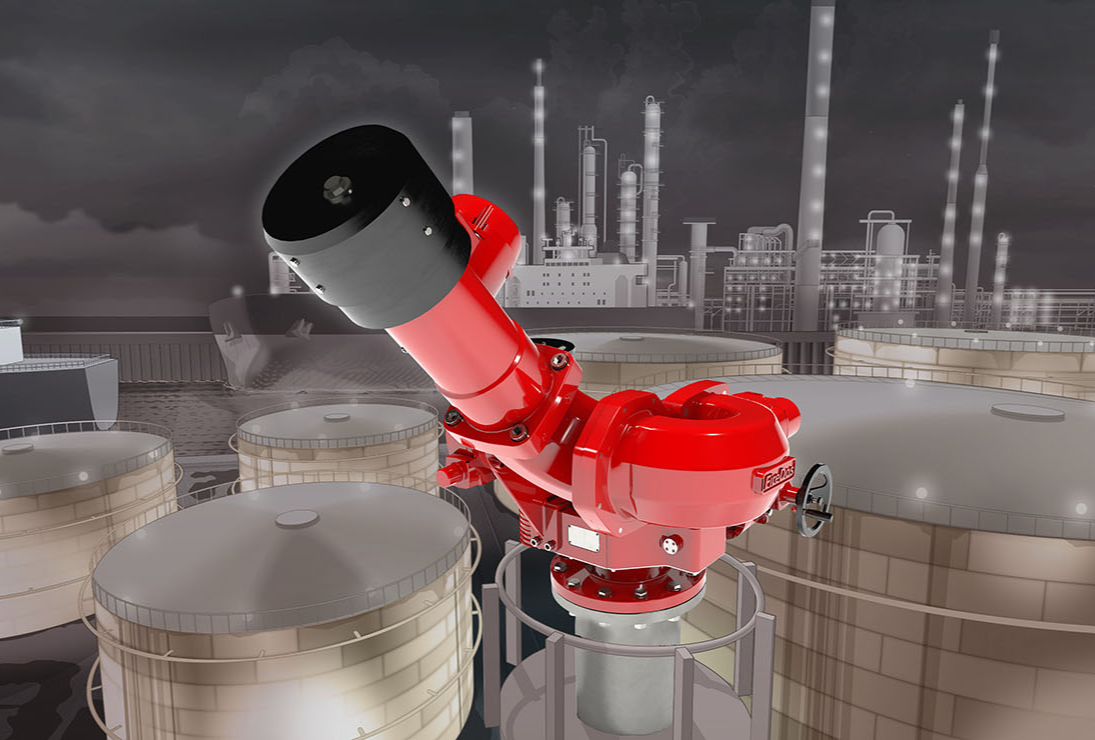
Monitors: Powerful and flexible
Thousands of liters of water per minute, reaching more than 150 meter.
View more