A GUIDE TO FOAM AND FOAM PROPORTIONING EQUIPMENT – PART 2
Following on from the first article we will now turn our attention to the effects of viscosity on foam proportioning.
Viscosity refers to a fluid's thickness or resistance to deformation. The higher its viscosity, the less is its ability to flow; the lower its viscosity, the more fluid (flowable) is the liquid. (Source: Wikipedia). Foam concentrates fall into one of two categories:
- Newtonian fluids – low-viscous, e.g. AFFF, Hi-Ex, Class A, multi-application foam agents.
- Non-Newtonian, pseudoplastic foam agents – high viscosity, e.g. AFFF-AR and SFFF (F3). However, not all SFFF or F3 foam concentrates are highly viscous.
Viscosity has a major influence on correct proportioning since the fluidity of foam can potentially affect accurate proportioning. This in turn can undermine firefighting effectiveness by producing a foam solution that is too weak: this relates to the importance of applying the correct application rate referred to in the ‘application rate matrix’.
Some key points to remember when choosing your proportioning system:
- Significantly higher pressure loss when using high-viscous foam concentrates, when compared to low-viscous foam concentrates, can rule out several proportioning technologies based on pressure ratios.
- Proportioning technologies using volumetric positive displacement pumps, such as plunger pumps or gear pumps, are most suitable for delivering high-viscous foam agents.
- The correct dimensioning of the suction line between the storage tank and the foam agent pump is crucial for correct proportioning.
Significantly, Factory Mutual (FM) have acknowledged the importance of these findings in their FM5130 standard, published May 2021. For the first time, specific and uniform approval requirements for a water-motor-driven foam pump proportioner have been established by FM. This covers
(i) Extended test point matrix, considering different pressure, flows and viscosities.
(ii) Overspeed scenarios such as 110% and 150% of Qmax.
(iii) 24h endurance tests. (Ref: FM Approval Standard FM5130 ‘Foam Extinguishing Systems’).
Critically, FireDos plunger pumps are specifically designed for pumping foam agents of all viscosities, in comparison with ‘off the shelf’ pumps used by competitors – these are designed for pumping fluids with properties similar to water. Gear pumps, which show good performance when run at high rotational speeds, have fixed flow rates and fixed back pressures. This means that they struggle in their efficiency when used with changing operating conditions such as flow range, backpressure and viscosity.
Varying operating conditions may cause problems with the proportioning rate when using gear pumps. Especially water-motor- or water-turbine-driven gear pumps operated at low flows and therefore low rotational speeds at the shaft. These show very poor efficiencies, especially at high pressures, making them hardly useable for sprinkler systems.
Depending on the viscosity of each foam concentrate used in specific applications, this results in a very different working range for the proportioner. FireDos Gen III proportioners offer a FM Approved working range from Qmin to Qmax of up to 1:15 (see FD8000/3-S which has a FM Approved working range of 137 gpm to 2113 gpm or FD20000/3-S with 351 gpm to 5284 gpm). With gear pumps in comparison, in many cases, Qmin to Qmax ratios of only 1:2 or 1:3 can be expected.

Design advice when using FireDos foam proportioners
- Consider pressure, flow and viscosity range, tested and approved by independent authorities.
- Design suction lines to be as simple and short as possible. Eliminate air traps. Consider temperature range and potential resulting viscosity increase in foam piping system design.
- Locate foam concentrate suction line connection at or near base of foam tank and of appropriate size.
- For high-viscosity foam concentrates try to provide a positive suction pressure at the pump suction inlet by raising the foam concentrate tank.
- Make sure that air entrapment at the foam concentrate is below 2%. Avoid any air entrapments in foam concentrate during manufacturing, transportation and filling processes.
- Consult foam manufacturers for foam concentrate and premix viscosities in order to be able to size and design lines properly.
If necessary, consider a reduced solubility in system design. - Test your foam proportioner regularly, preferably without producing premix or foam.
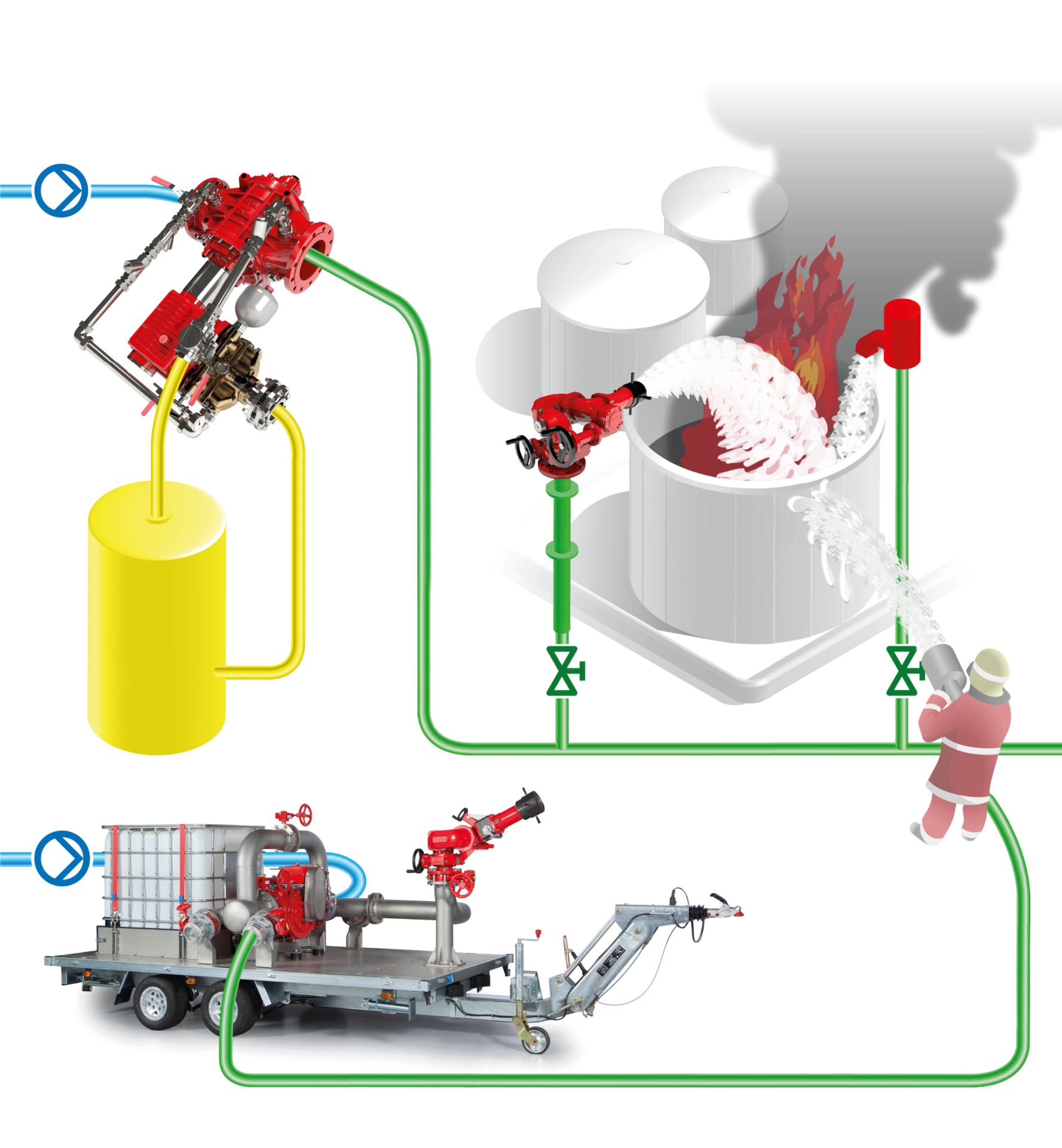
Stationary proportioner, monitor and fire trailer, equipped with proportioner and monitor
Typical foam application areas and recommended discharge devices
The examples below are typical of the fire scenarios found on the majority of high-hazard sites. The main objective is to bring the most appropriate type of foam to the application (either low, medium or high expansion), combined with the most appropriate discharge device; that could be sprinkler, overhead deluge, low level medium expansion pourers, high expansion generators or foam monitors. However, the use of foam in fire suppression is not limited solely to the traditional process industries. There are equally valid applications in industries such as aviation and aircraft hangars, energy from waste/waste recycling centers, ship jetties and the ships themselves. We have separate introductory guidance documents via our website. If we were to summarize the best approach to any fire challenge it would be that all parties should engage with the risk assessment process in partnership with suitably qualified and experienced personnel.
The most common areas of firefighting with foam are:
Process areas: this includes the array of vessels, pipes, and tanker loading/offloading.
Overhead foam deluge or fixed foam monitors is standard practice in this environment. Overhead foam deluge will apply a low expansion foam blanket to both vertical surfaces (through run-down of foam) and to low-level bunded containment of plant. Process plant is usually on several levels
with open grided flooring. Nozzles can be fixed to target the areas around vulnerable vessels whilst draining down to blanket product at ground level. Minimum application rate of 0.16 gpm/ft2. Fixed foam monitors are sometimes preferred as they can be more cost effective. They
are mounted externally to open process plant and so avoid the installation of the internal pipework needed to supply deluge nozzles. However, monitor nozzle efficiency is the key to success to avoid the effects of wind deflection. Commonly, trailer-mounted monitors and proportioners in
combination with hose-laying equipment are used as backup systems. FireDos have a range of monitors with this in mind. They have a unique ‘oval-flat’ design. This optimizes the laminar flow to achieve industry-leading range on both jet and spray. Depending on the local challenge, FireDos
offer monitors that will deliver both unaspirated and aspirated foam or water only. Needless to say, all materials are seawater compatible and suitable for harsh atmospheric and marine environments. Minimum application rate of 0.25 gpm/ft2.
Storage tanks and bunds: both for finished product and the bulk solvents needed for the product formulations.
Storage tanks typically have one of three main roof types. These are fixed roof, internal floating fixed roof and floating roof. Whilst each require a specific method for applying foam, all three are ideal for FireDos water-driven foam proportioners as the key piece of infrastructure.
Both fixed roof and internal floating roof tanks require tank pourers mounted into the side wall of the tank and apply foam to the surface of the product. The aspiration of the foam is through air entrainment at the pourer, as with overhead foam deluge the finished foam is classed as low
expansion. Minimum application rate of 0.1 gpm/ft2. Floating roof tanks have a platform which rises and falls as product levels rise and fall. The key area for fire suppression is the seal between the platform and tank wall. The floating roof tank pourers are mounted around the
circumference of the tank to discharge low expansion foam only within the confines of a low level rim-seal dam, this prevents loss of foam across the internal diameter of the tank. Minimum application rate of 0.3 gpm/ft2. In the case of full surface fires, trailer-mounted
monitors and proportioners in combination with hose-laying equipment can be effectively used as support and/or backup systems.
Bulk stock: typically held outside in intermediate bulk containers (IBCs) and in bunded areas or in 55-gallon drums in a warehouse.
Using the same FireDos water-driven foam proportioner infrastructure, pipework can be installed to allow fixing of medium expansion foam pourers at low level around the bund perimeter. Medium expansion foam is created by greater aspiration at the pourer than that for foam deluge nozzles.
The key benefit is enhanced levels of vapor suppression through the creation of a deeper blanket. The system has the added benefit that it can be activated to prevent ignition following a major spill. Minimum application rate of 0.1 gpm/ft2. With internal warehousing and the
potential for high rack storage, overhead and in-rack foam enhanced sprinklers are considered to be minimum protection. Depending on the product flashpoints and degree of water solubility, it may be necessary to install overhead foam deluge along the same lines as for the processing plant.
Minimum application rate of 0.16 gpm/ft2 for foam deluge.

Typical foam application areas
Site fire teams
Larger sites such as refineries usually have a well-equipped fire team. They complement fixed systems with a well-trained crew providing a flexible solution. Despite the most comprehensive risk assessments, fire scenarios are not always predictable. Site fire teams will depend on their equipment to perform in very demanding situations and both FireDos foam proportioners and foam/water monitors are fitted extensively to fire trucks. The foam proportioners are either embedded in the appliance itself or can be fitted to specialist foam trailers for separate deployment. Likewise, monitors can be either cab mounted or trailer mounted together with a FireDos foam proportioner.
Summary
Whilst we have attempted to cover many of the most frequently encountered foam-related applications, we are aware that it can be a complex subject. As we highlighted at the start, fire hazards are classified in relation to their extinguishing methods. However, when it comes to larger inventories of flammable liquids, we are certain foam is the most effective. Moreover, proportioning and applying foam is our area of expertise. We can provide informed advice through our network of North American Authorized FireDos Distributors. We look forward to working with you.
this might also be of interest for you:
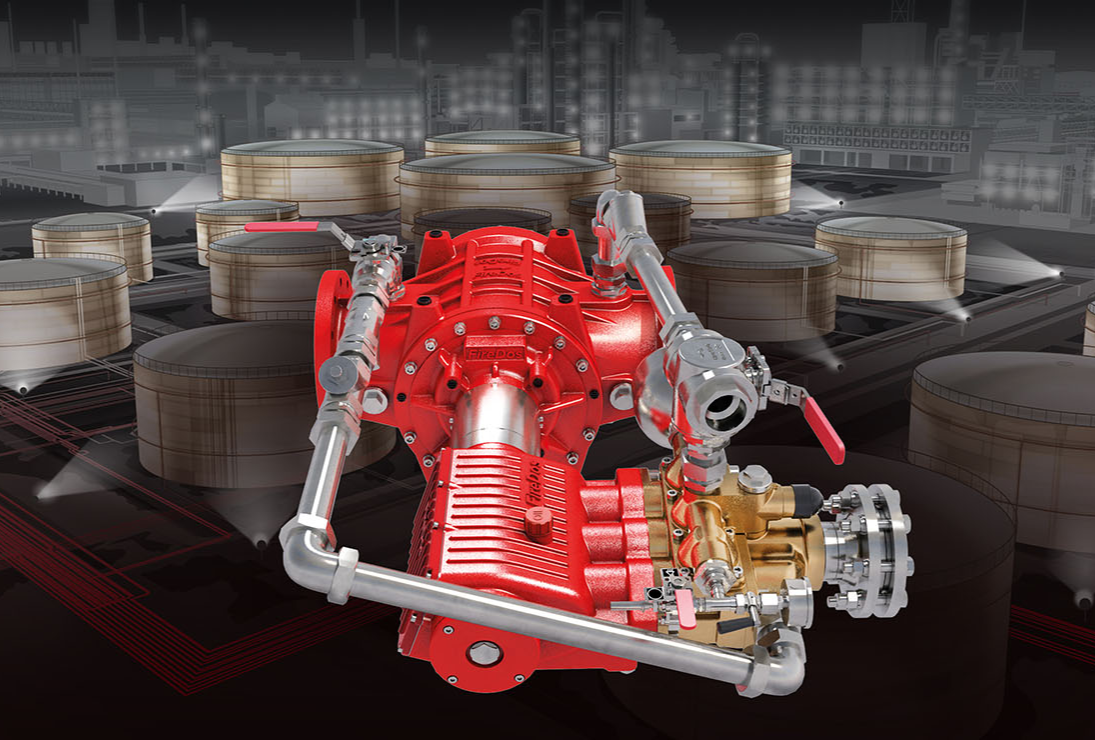
stationary foam proportioners
Increase performance, save costs: Learn more about the advantages.
View more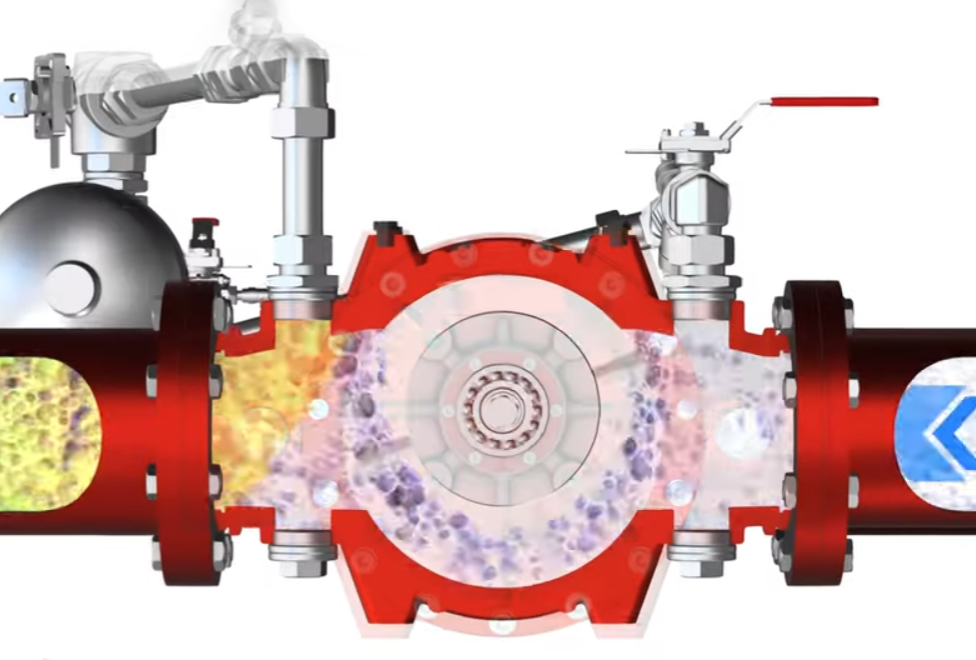
Extinguishing agent and technology: What you should know.
We have compiled interesting facts around these topics.
View more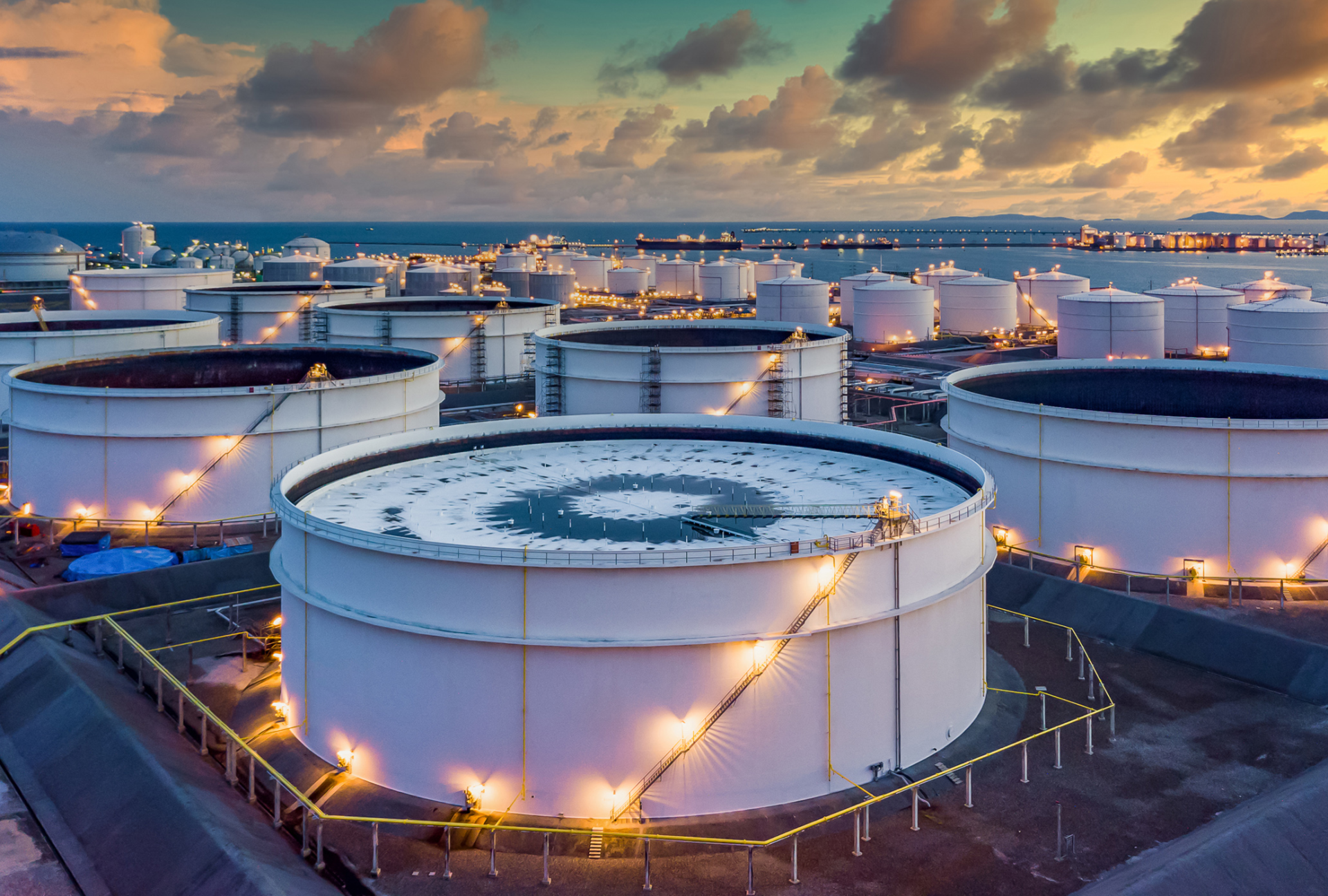
our solutions for tank farms
Learn how to reduce risks with a flexible fire protection concept.
View more